Uploading Files
To upload files to the Prusa Printers first get the stl, obj, or other 3D file type and open it with PrusaSlicer either through opening through File Explorer or dragging the file into the PrusaSlicer application, or clicking the (
) icon and selecting the file.
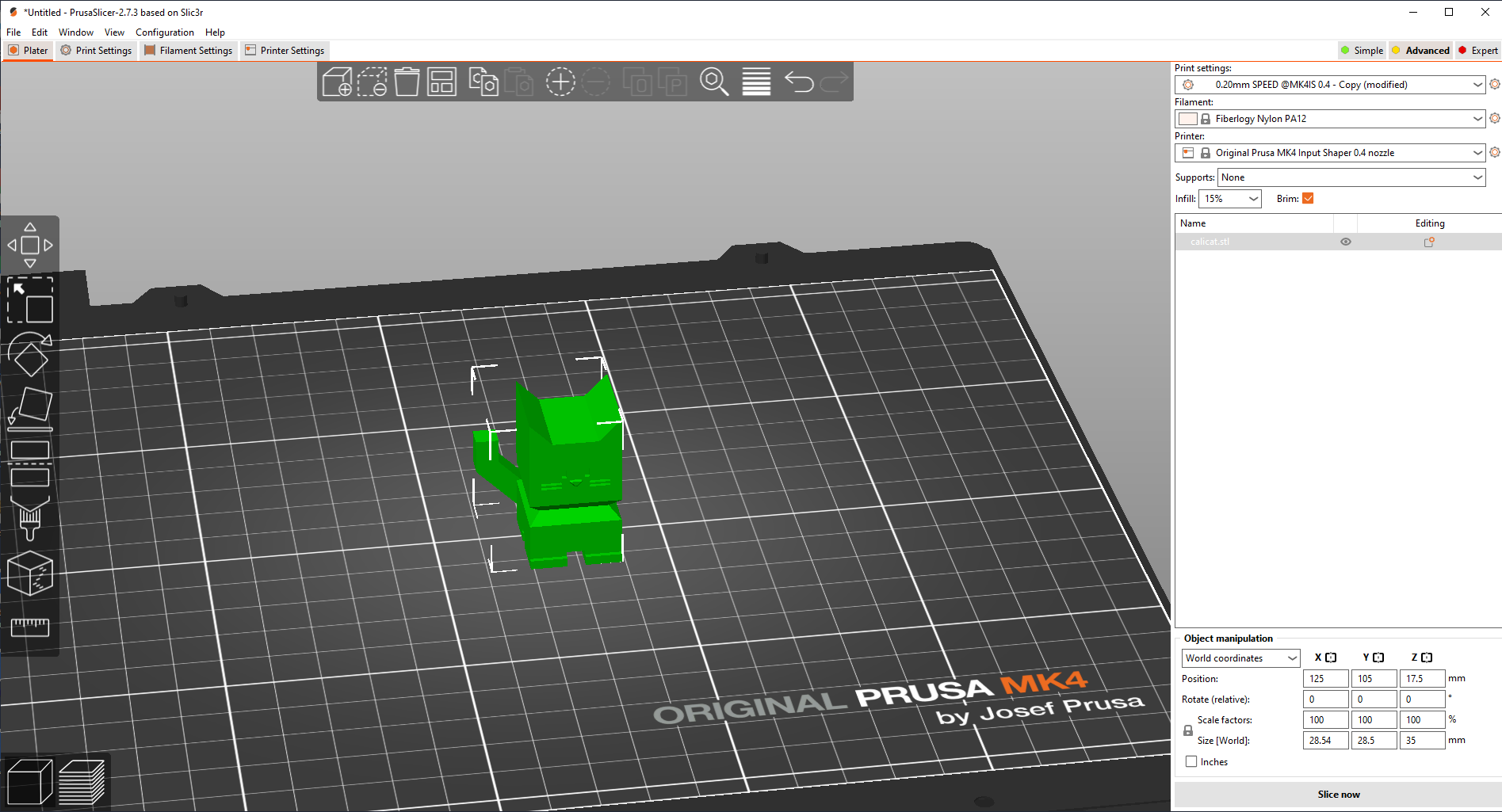
Once the file loads in, you can move it around the buildplate and change it to your likings, or upload more files by dragging them into the application window.
In the top menu you will see a list of options.
(
) will allow you to add a file from file explorer
(
) will delete the current selected object
(
) will clear the buildplate of all objects
(
) will arrange the models on the buildplate
(
) will copy the selected object
(
) will paste from the clipboard
(
) will add a copy of that object
(
) will remove a copy of that object
(
) will split a separated object into multiple objects
(
) will split a separated object into multiple parts
(
) will let you search features
(
) will bring up the variable layer height
menu which is beyond the scope of this guide and should not be used without a more comprehensive understanding of the printers.
(
) undoes the last action
(
) redoes the last undo
Moving
To move the print around the print bed, first click the item you wish to move, then either drag your shape to its intended position, or click the (
) icon and you will see three arrows pop up around your shape.
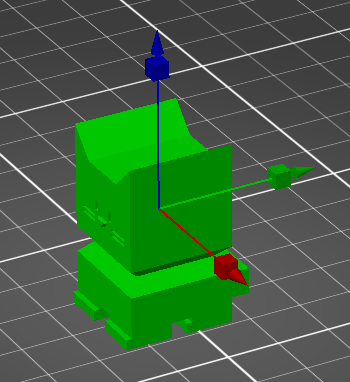
Once that happens you can either move it on the main axis by dragging those arrows, or just grab and drag the object to wherever you want it.
You can also set its exact position with the menu on the bottom right of the screen.

There you will also see a menu with two options World Coordinates
and Object Coordinates
.
World Coordinates
lets you set position relative to the bed, with 0,0 being at the bottom left corner.
Object Coordinates
lets you shift the object from its current position and will move it as far as you put in. You can also switch to measuring in inches by checking the inches box.
Scaling
To scale your object, select the object, then select the (
) icon, and three lines with boxes will appear, as well as a few orange boxes in a square around it.
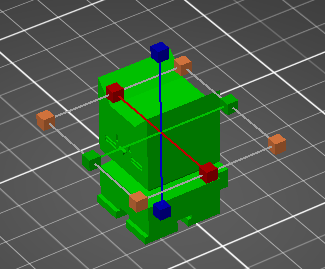
You can grab any of the three to stretch the object in the direction of that line, or instead grab one of the orange boxes to stretch in all directions equally.
You can also set its exact scale with the menu on the bottom right of the screen.

Scale Factors
allows you to set the scale relative to the original object.
Size \[World\]
allows you to set the numeric size along all three axis. You can also switch to measuring in inches by checking the inches box.
If the lock icon is closed, the object will retain it’s original proportions and scale axis equally. If it is open you can manipulate the three separately.
The rewind icon will set the object to it’s original dimensions.
Rotation
To rotate your object, select the object, then select the (
) icon, and three rings will appear.
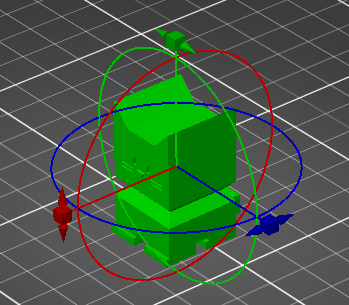
You can grab these rings and rotate them to rotate the object how you would like it to print. Keep in mind where the front of the bed is, signified by where it is written Prusa MK4
.
It is recommended to rotate the object so that the least amount of overhang is achieved:

And the maximum amount of the print is touching the build plate:
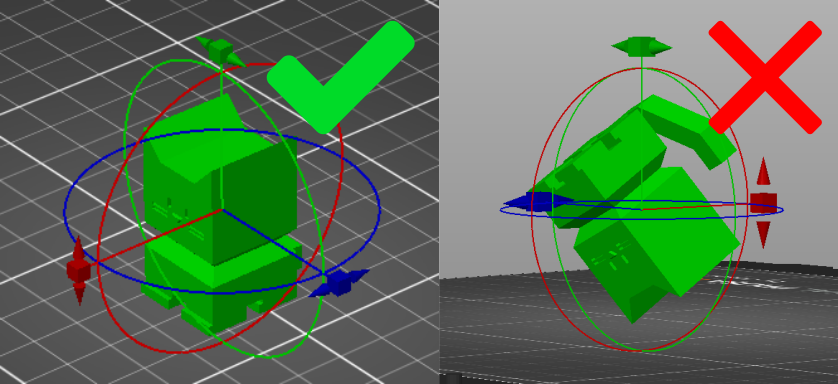
You can also set its exact rotation with the menu on the bottom right of the screen.

Putting numbers in the text boxes will rotate the object in the direction of the arrows that appear as many degrees as you insert in the box.
You can also click the (
) icon and your object will show white planes. Clicking one of these will orient the object so that the selected plane is touching the buildplate.
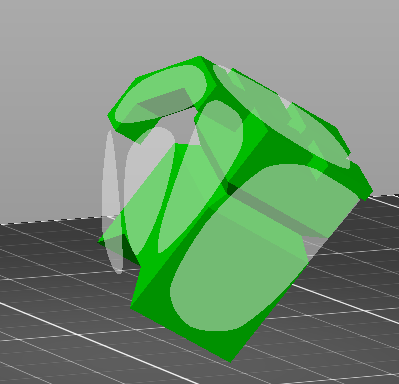
Cutting
To cut your object in 2 pieces, hit the (
) icon, and a menu will appear, as well as the cutting plane.
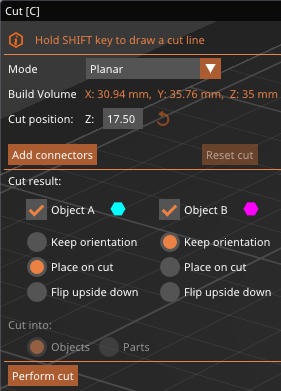
In the menu you will see a selection box labeled Mode
. Inside there are two options, Planar
and Dovetail
.
Planar
When you select planar, you should first select where you would like to cut the file. The plane will automatically appear and shade the two halves of the object different colors. To adjust this cut, you can either drag the red and green arrows to tilt the plane, or grab and drag the grey ball to move the plane.
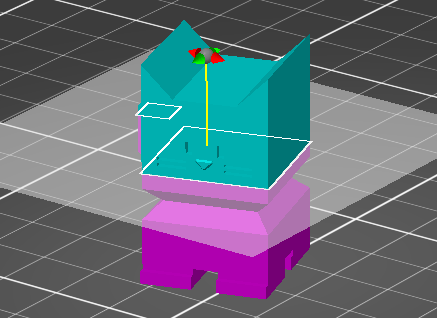
You can also set the height of the cut off of the buildplate automatically in the menu.

This will create a smooth cut into two pieces.
If you want to instead have a more secure way of joining these pieces after you cut, press the Add Connectors button.
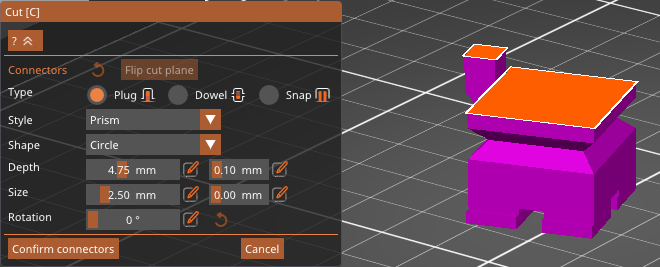
From there it will hide one of the two halves, and allow you to place connectors. You will see 3 options for the type of connector, Plug
, Dowel
, and Snap
.
Plug creates a small protrusion from one side, and a matching hole in the other. You can select whether you would like a prism
or frustum
shape:
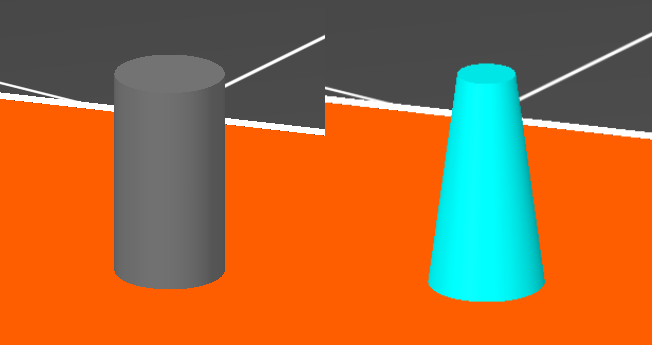
As well as what shape you would like it to be, triangle
, square
, hexagon
, or circle
:
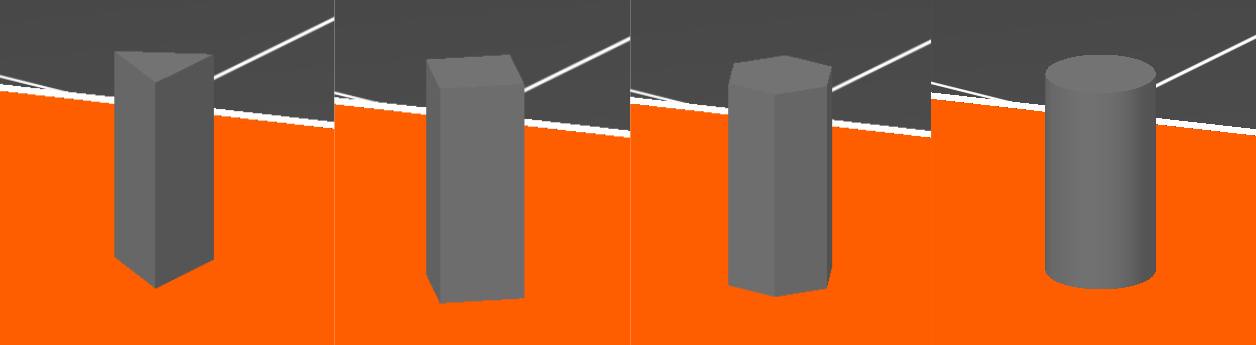
Dowel creates holes in both halves of the print as well as a small dowel to join the two.
Again you can choose the shape of the dowel, triangle
, square
, hexagon
, or circle
:
Snap creates a small mechanism which will snap into a hole in the other piece.
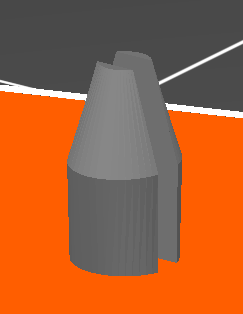
For all of these options, you can change the depth out of or into the piece, the horizontal size of the peg, and the rotation around its center.
For the snap you can alter the bulge of the top section and space between connectors. Hitting the rewind icon will pu tit back to default settings.
Once you are happy with the settings, you can click anywhere on the orange surface to place the connector where you click.
Hit confirm connectors
once you are happy with the connector position and settings or cancel
to return to the cut menu.
Dovetail
Dovetail will create a unique joint between the two pieces, where one will be able to slide into the other.
The plane will automatically appear and shade the two halves of the object different colors. To adjust this cut, you can either drag the red and green arrows to tilt the plane, grab and drag the white ball to rotate the groove, or grab and drag the grey ball or cube to move the plane.
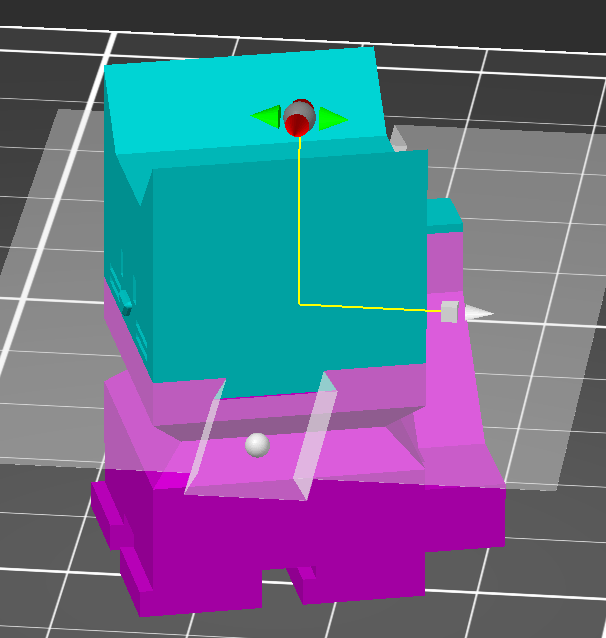
You can also set the height of the cut off of the buildplate automatically in the menu.

From there you can adjust the settings of the dovetail joint, with the sliders provided. Hitting the rewind icon on any slider will set that slider back to it’s default position.
Cut Result
Below the other settings, you will see a section named Cut Result
. There you will see a column for each half of the cut. If the check box is selected the cut will generate that pice and not discard it.
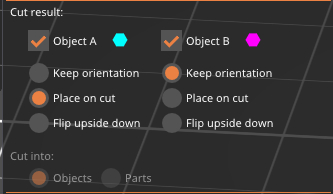
You can then select how to place the object once it cuts. Keep Orientation
will keep the object as it is before that cut. Place On Cut
will lay the object along the plane of the cut. Flip Upside Down
will invert the object.
If you have selected planar and not added connectors, you can at the bottom select to cut into parts instead of objects, which will leave the two sides connected but allow them to have their settings edited separately with the left parts menu.
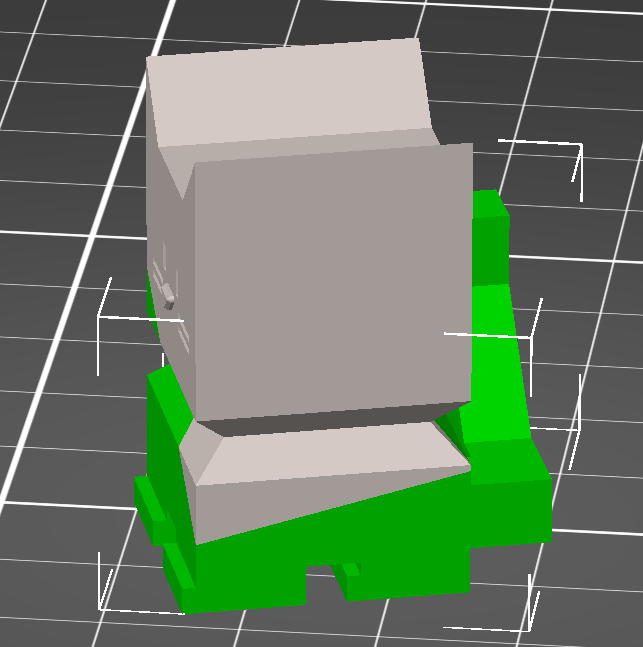
Support Painting
If you press the (
) icon you can add supports in specific spots by “painting” with your mouse. Click and drag to add supports where you drag, and right click and drag to block supports in the certain spots you “paint”.
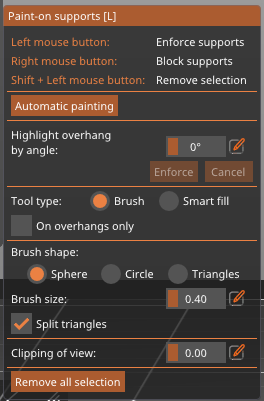
You can also automatically paint areas, edit where can be painted, and edit your “brush” shape in the menu below.
Seam Painting
If you press the (
) icon you can control where each layer of the print starts and ends, creating a small slightly visible seam.
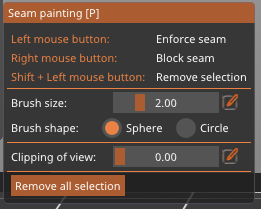
Clicking and dragging will force the printer to place a seam there, and right clicking and dragging will stop seams in that area.
You can also change the shape of your brush and view options in the menu that appears.
Measuring
To measure your object, select the object, then select the (
) icon. You can then click individual faces, edges, and points to measure the distance, angle, and areas of the parts selected.
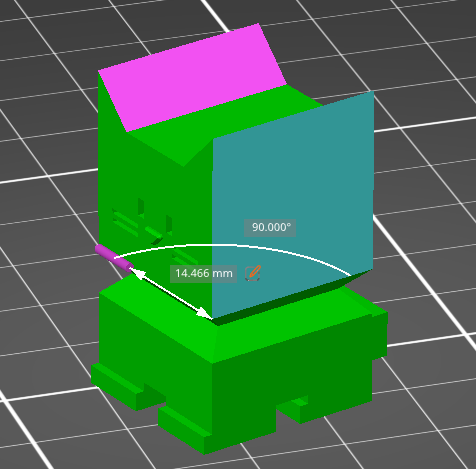
When you measure a length, a (
) icon will appear, and allow you to change the length highlighted and scale the rest of the model to enforce that length.
In the menu you can either hit the Restart Selection button to clear your selection, or click the (
) icon next to the measures to copy the numbers there.
Done?
Once you are happy with the object’s placement, move to the Printer Settings section.
Printer Settings
Once you are satified with the object placement, move to the right menu.
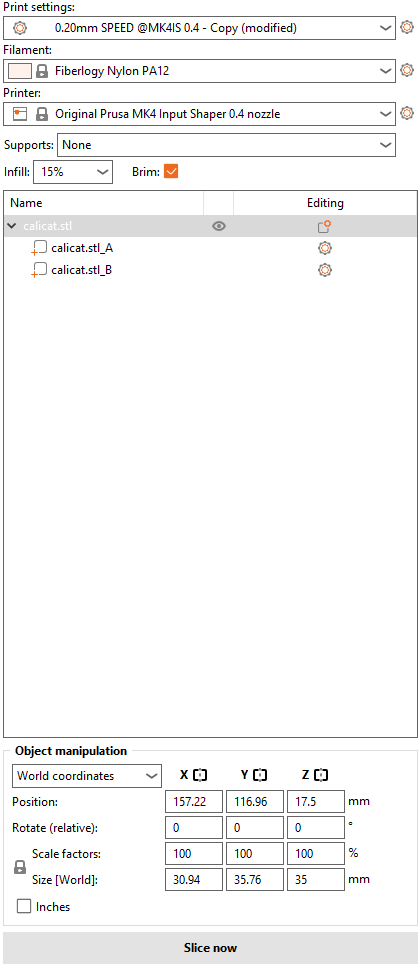
Print settings
Here you will see a list of settings for layer heights:
0.1 mm will be the most precise setting, good for visual detail or mechanical functionality.
0.15 mm has both SPEED and STRUCTURAL options, choose SPEED for a faster print, or STRUCTURAL for a sturdier print.
0.2 mm has the same options, but both will be faster but lower quality than their 0.15 mm counterparts.
Filament
Here you can select the type of filament to be printed. Make sure this matches what is loaded in the printer before printing.
Printer
Here you select which printer to use. Select Original Prusa MK4 Input Shaper 0.4 nozzle.
Supports
Supports are how the printer helps overhangs print, as the printer must always work from bottom to top and cannot print without a surface to print on. Support can be selected and deselected, but is recommended to use whenever there are overhangs or floating objects in your print.
The options in the dropdown designate where supports generate, and gives 4 options, None
, Support on Buildplate Only
, For Support Enforcers Only
, and Everywhere
.
None
will not create any supports.
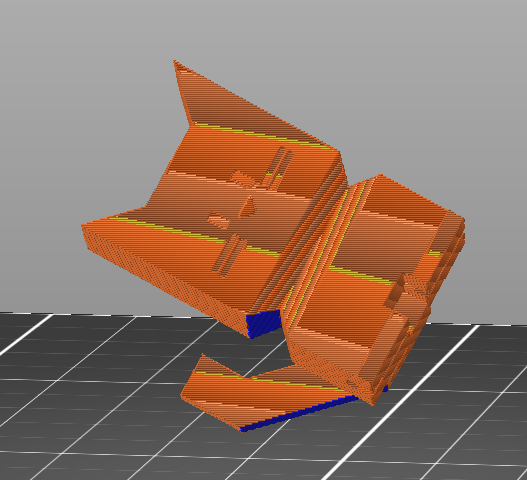
Support on Buildplate Only
will only support overhangs over the buildplate, and overhangs that have other bits of object below will not generate support.
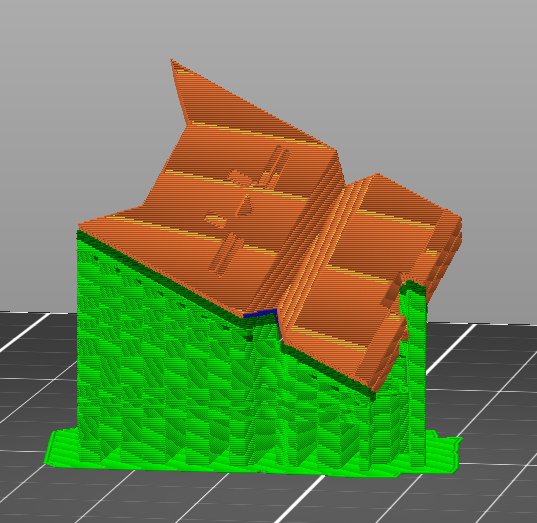
For Support Enforcers Only
only puts supports in specified spots, either by you or the model itself.
Everywhere
means any overhang will be supported, no matter where on the print it is.
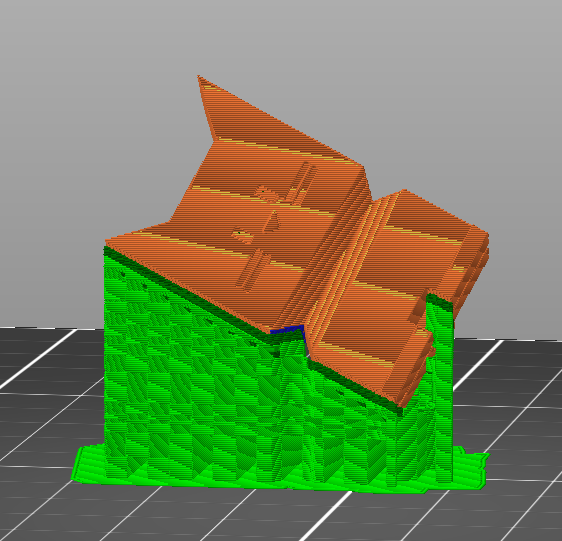
It is recommended to use Everywhere
when overhangs are present.
Infill
This will allow you to dictate how much of the interior of the print is filled in, with 0 meaning no fill, and 100 meaning completely full.

Anything down to 10%
will be self supporting enough, although 20%
is recommended for nearly every print. 70%
is the absolute maximum you need to go for a high strength print, however this should only be used if extreme strength is needed.
Brim
The brim helps prints stick to the print bed and avoid shifting and warping off of the bed. It is recommended to keep this setting selected for any print.
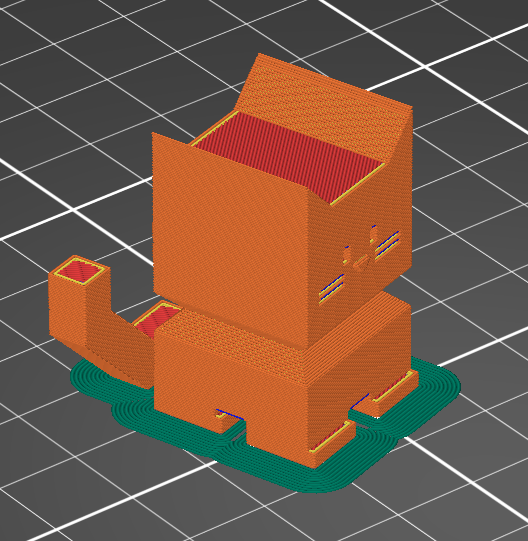
Part Specific Settings.
In the part menu, you can select and change settings for specific parts by clicking the (
) icon.
The full scope of this will not be covered on this website.
Custom Settings
In the top left you will see tabs wil more settings. These can affect more specific things about the print and printer but that is only recommended to use if you are more comfortable with the printer and how it works.
Done?
Once your settings are as desired, move to the Slicing Files section.